Why is process safety management certification a necessity for your workplace safety?
If you are involved in a company that stores, uses, or produces hazardous chemicals, proper management is vital to your life. In such situations, the process safety management course comes to your aid.Â
This certification course is essential for companies with greater workplace hazards. Now let’s understand the proper definition of process safety management.
What is process safety management?
Process Safety Management (PSM) is a disciplined framework based on OSHA standards that emphasizes the importance of managing the integrity of operating systems and processes that handle hazardous substances.
Don’t let the technicalities get to your head. Its primary goal is to prevent unplanned releases of hazardous materials or energy, which could lead to a major incident.
This course teaches employers how to identify, evaluate, and control the hazards associated with the risk of unexpected releases of toxic, reactive, or flammable liquids and gases used in their processes.
It’s a shocking fact that 56 process safety events took place between 2007 and 2017, which led to 128 deaths. This underlines the importance of process safety management certification. Ensign Academy is a noteworthy institution that provides a Nebosh HSE certificate in Process Safety Management.
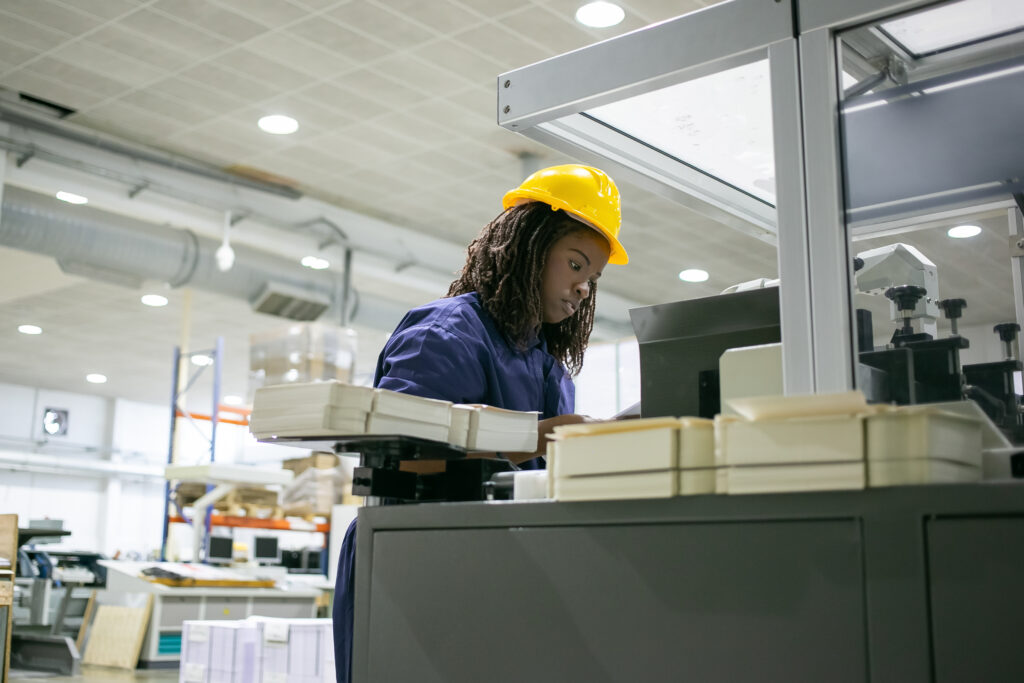
Importance of Process Hazard Analysis (PHA)
The PHA is an integral component of an effective process safety management program. It is required for employers to conduct a thorough analysis of the entire operating process. This assessment is known as process hazard analysis, or simply PHA.
To successfully run Process Safety Management programs, OSHA requires PSM programs to contain the following 14 key elements:
- Process Safety Information
Before performing a PHA, employers must create written safety information about the hazards of the chemicals and tools they are using on the job. - Process Hazard Analysis
Employers need to recognize, assess, and manage potentially dangerous processes. But the fact is, organizations can’t manage safety and hazards until they know what hazards are actually in their facilities. - Operating Procedures
Employers are advised to develop and implement written operating procedures. All we need is a consistent, well-established safety protocol. - Incident Investigation
When an incident occurs during the process, thorough investigations must be conducted, and businesses should record, track, investigate, report, and analyze what happened. - Management of Change
To ascertain whether there will be any effects on the health and safety of employees, changes to a process must be assessed. - Mechanical Integrity
Correct installation and design are required for process equipment. It is important to evaluate the evolving safety risks of equipment. - Employee Participation
PSM programs must be implemented by the employer, and all employees should participate. To do so, employees can access, acknowledge, and sign off on policy documents. - Trade Secrets
Employers must provide thorough documentation of materials and processes to comply with PSM standards, regardless of whether the information is a trade secret. - Compliance Audits
Internal audits must be calculated and reported at reasonable intervals to ensure procedures and processes are compliant. - Training Management
Employees should be given effective training on all safety procedures and have access to ongoing refresher training. - Contractor Safety Management
All contractors who work with or near highly hazardous chemicals must be trained in emergency procedures and other PSM-related aspects. Therefore, process safety management systems should address the safety of contractors and subcontractors. - Hot Work
Hot work permits are required for any hot work operations or other sources of ignition occurring near the process. Hot work permits are a systematic process for authorization and oversight when there is a firework. - Pre-Startup Safety Review
The PSSR must be conducted for new and modified facilities before any hazardous substances are introduced into the workplace. - Emergency Planning and Response
Employees must be trained in emergency planning and response procedures if something goes wrong.
These are the 14 golden tips for implementing process safety management in the workplace. It is also worth noting that Process Safety Management is complicated and necessitates a multifaceted approach that combines technology and management solutions.
Implementing PSM at your workplace: How?
Implementation of process safety management can be done in different ways. Some businesses will follow a traditional approach. They will manually enter the data into spreadsheets or fill out internally created forms. Even though it looks like an economical approach, it’s very time-consuming and prone to human error.
Others employ PSM specialists and consultants to visit the site as needed. However, this can get pricey, especially if you need to evaluate several processes.
PSM software, which can perform most of the work for you, may be a better option. Software systems can ensure compliance, speed up the process, and assist in identifying and reducing risks.