10 Tips No One Tells You About Identifying Workplace Hazards
Anytime a hazard can happen! especially in a manufacturing plant or in the chemical industry. So it is better to implement workplace safety to avoid imminent hazards.
Depending on the size of the industry, the risk of workplace hazards may increase. The larger the industry, the more mechanical the processes, and the greater the demand for qualified safety specialists.
How to identify hazards in the workplace?
The solution is here. Just follow these tips and practices to identify workplace hazards.
Let’s dive in.
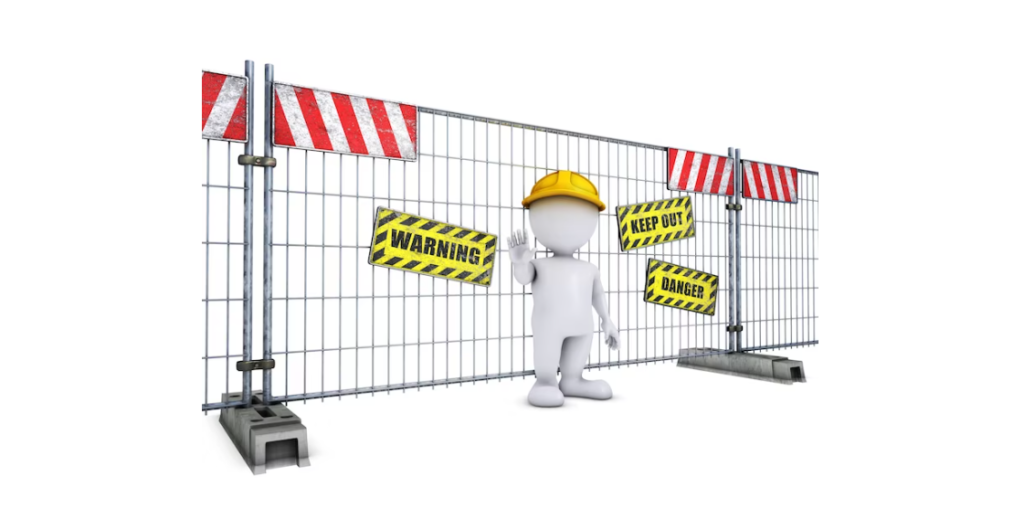
Types of hazard identification methods
There are several effective methods for identifying workplace hazards. The following are some common types of hazard identification methods:
- Workplace Inspections: Regular workplace inspections can help identify hazards. To identify potential hazards, trained individuals such as supervisors, safety officers, or designated safety teams visually assess the work environment, equipment, processes, and practices.
- Job Hazard Analysis (JHA) or Job Safety Analysis (JSA): This method entails dissecting each job or task into individual steps and analyzing the potential hazards associated with each step. JHA/JSA assists in identifying specific hazards and developing appropriate controls by systematically reviewing the tasks, equipment, and materials involved.
- Incident and Accident Investigation: Analysis of previous incidents, accidents, and reported hazards can provide valuable insights into potential hazards in the workplace. Investigating these events aids in identifying root causes and underlying hazards, allowing for corrective actions to be taken.
- Safety Data Sheets (SDS): SDS, also known as Material Safety Data Sheets (MSDS), are documents that contain information about the hazardous properties, handling, and safe use of chemicals and substances commonly found in the workplace. An SDS review can assist in identifying potential hazards associated with specific substances.
- Employee Consultation: Involving employees in hazard identification can be an effective strategy. Employees frequently have firsthand knowledge of potential hazards and can provide useful insights and recommendations. Open communication and involving employees in safety discussions and inspections can help to improve hazard identification efforts.
- Hazard Checklists and Templates: Using standardized checklists and templates tailored to specific work environments, industries, or tasks can help systematically identify common hazards. These checklists frequently cover a wide range of hazard categories, including physical, chemical, biological, and ergonomic hazards.
- Industry-Specific Regulations and Standards: Many industries have specific workplace safety regulations, standards, and guidelines. Following these guidelines can assist in identifying hazards and ensuring compliance with industry-specific safety protocols.
- Technological Solutions: Advanced technologies such as hazard monitoring systems, sensors, and data analytics are great for identifying hazards. These tools are capable of detecting abnormal conditions, monitoring air quality, temperature, noise levels, or machine performance, and providing early warnings of potential hazards.
Point to remember: Combining these methods can provide a more comprehensive approach to hazard identification. Each method has advantages and disadvantages, and organizations should tailor their approach to their specific needs and industry requirements.
How can we avoid workplace hazards?
Controlling workplace hazards is critical for ensuring employee safety and well-being. Here are some golden tips to help you effectively control workplace hazards:
- Conduct a thorough risk assessment: Conduct a comprehensive risk assessment to identify potential hazards in your workplace. Examining the tasks, equipment, and processes involved, as well as determining potential risks and their severity, are all part of this process.
- Implement safety protocols and procedures: Create and enforce clear safety protocols and procedures for each task and operation in your workplace. These should include equipment safety guidelines, hazardous material handling procedures, and emergency response plans.
- Training and education: Make certain that all employees are properly trained and educated on workplace hazards and safety procedures. Training sessions on hazard identification, safe work practices, proper use of personal protective equipment (PPE), and emergency protocols should be included.
- Keep your workplace clean and organized: Maintain a clean, clutter-free, and well-maintained workplace. To reduce the risk of accidents or malfunctions, inspect and maintain equipment regularly. Store hazardous substances and materials properly to avoid spills or exposure.
- Implement engineering controls: Use engineering controls to reduce workplace hazards. This could include installing machine guards, installing ventilation systems to control airborne contaminants, or implementing noise reduction measures.
Engineering controls are effective when used to redesign processes by putting a barrier between people and hazards or removing hazards from people. Such processes include machinery guarding, proximity guarding, extraction systems, and removing the operator to a remote location far away from the hazard.
- Encourage open communication: Create an open communication culture where employees are comfortable reporting hazards or potential risks. Create a system for reporting and responding to safety concerns as soon as possible.
- Regularly review and update safety policies: Because workplace hazards can change over time, it is critical to review and update safety policies and procedures regularly. Keep up to date on new regulations, industry best practices, and emerging hazards in your workplace.
- Conduct regular safety inspections: Conduct routine inspections to identify and address potential hazards. Encourage employees to take part in inspections and report any issues they encounter.
- Promote a safety-conscious culture: Establish a safety-first workplace culture. Recognize and reward safe behaviors, involve employees in safety committees or meetings, and instill a sense of shared responsibility for safety among all employees.
- Personal protective equipment (PPE): Personal protective equipment (PPE) is regarded as the final step in the risk-reduction process.
Gloves, spectacles, earmuffs, aprons, safety boots, and dust masks are all examples of common PPE that are specifically designed to reduce exposure to the threat.
Identify the personal protective equipment required for various tasks and provide employees with the necessary gear. Employees should be educated on the proper use, maintenance, and limitations of personal protective equipment (PPE).
Wrapping Up
Even a small accident could have catastrophic effects on the entire industrial operation. Safety experts must assess risks and foresee challenges to ensure a smooth industrial operation. Once a threat has been identified, it should be evaluated and calculated for strategies to be implemented.
Keep in mind that reducing workplace hazards is an ongoing process. You can reduce risks and create a safe and healthy work environment for everyone by remaining vigilant and proactive.